Free ShopCare resources to help improve your HSW outcomes
The following free resources provide up-to-date HSW guidance and include practical tools designed specifically for the retail sector and its supply chain.
We have created a series of webinars to help you achieve better health, safety, and wellbeing outcomes. Click here to view our YouTube channel: ShopCare – YouTube
Read our latest releases with in-depth analysis of workplace health and safety trends across retail, manufacturing, transport, logistics, and wholesale sectors.
Click to view:
Find out more about the data and insights available to you here.
ShopCare case studies
These case studies have been developed collaboratively in New Zealand, to illustrate real-life solutions to local situations.
ShopCare supports the retail sector and its supply chain with knowledge transfer and industry collaboration. If you have any questions, please don’t hesitate to contact the team.
How to use these case studies as a learning opportunity:
- Read and examine the case thoroughly. Take notes, highlight relevant facts, and underline key problems.
- Focus your analysis. Identify two to five key problems.
- Uncover possible solutions.
- Select the best solution.
Faced with a rise in manual handling injuries, Harvey Norman partnered with ShopCare to try something different – putting workers at the centre of the solution.
This case study explains how a co-designed ergonomics pilot, shaped by frontline staff, delivered practical changes like redesigned trolleys, new training approaches, and early discomfort reporting. The result: a 40% drop in ACC claim costs and zero ergonomics-related incidents since rollout.
Thanks to Harvey Norman, we can share a proven model that other organisations can adopt – combining worker input, smart design and practical tools to transform safety outcomes.
Read how Harvey Norman used co-design to reduce injuries and embed safer practices.
This case study showcases a practical, proven approach from Industry Med that has improved return-to-work and recovery-at-work outcomes in a rural manufacturing setting.
Industry Med demonstrate how a coordinated, holistic healthcare model with onsite and virtual clinic support can support better outcomes for workers, businesses, and the wider system.
Whether your business has an established return-to-work programme or is just starting out, this case study offers useful insights into what’s working, and can be applied across other industries.
Read about the innovative solutions that Industry Med put in place.
ShopCare in collaboration with Toll Global Express, developed the following video case study to showcase to the wider community, an example of industry good HSW practice in action. We encourage you to watch the entire case study and focus on the key takeaways for you and your organisation.
Some key themes are embedded throughout the case study such as safety leadership, safety culture, effective site design, use of data trends and ensuring workers are engaged in processes and change. We recommend that you undertake some additional research on these themes that meets your individual/business needs.
Watch the video here and see the companion document for additional information and useful links.
Approximately 30,000 pallets of product are delivered each week to Foodstuffs South Island Christchurch distribution centre. The challenge was understanding the factors contributing to increased incident reporting of product damage and near misses within the distribution centre through a comprehensive corrective action plan.
A team including health and safety representatives, suppliers, supervisors, and management worked together to understand how the four key factors contributed and to find solutions.
Learn how they significantly reduced near misses and reduced product damage by 30%.
The Executive team and Board wanted to understand the top critical risks within the business and what control measures were required to keep employees, customers, clients, contractors, and visitors safe.
Among other benefits, introducing traffic management plans across the business, including driver safety and exclusion zones, resulted in a 50% reduction in incidents over a rolling 12 month period.
Understand how they achieved the improvements in their processes
Foodstuffs North Island has 2,500 stores and 24,000 employees. The injury management process was not being utilised as intended, leading to delays reporting incidents. The programme was refreshed and called ‘Back In Action’, providing a simple, transparent process for employees and managers to follow.
The programme works so well that they now advise health providers about an injury and provide the paperwork before an employee arrives at their clinic.
Comvita has had a considerable reduction of incidents over the last four years since starting their health and safety journey. Their beekeepers’ competency and capability have increased to the point that they now have “in-house” champions providing guidance and support to new members of the team.
Comvita has seen a change to a more proactive approach to ensuring each vehicle, plant or piece of equipment is safe to use and remains fit for purpose.
Read how engaging the teams directly led to the reduction of incidents within the fleet
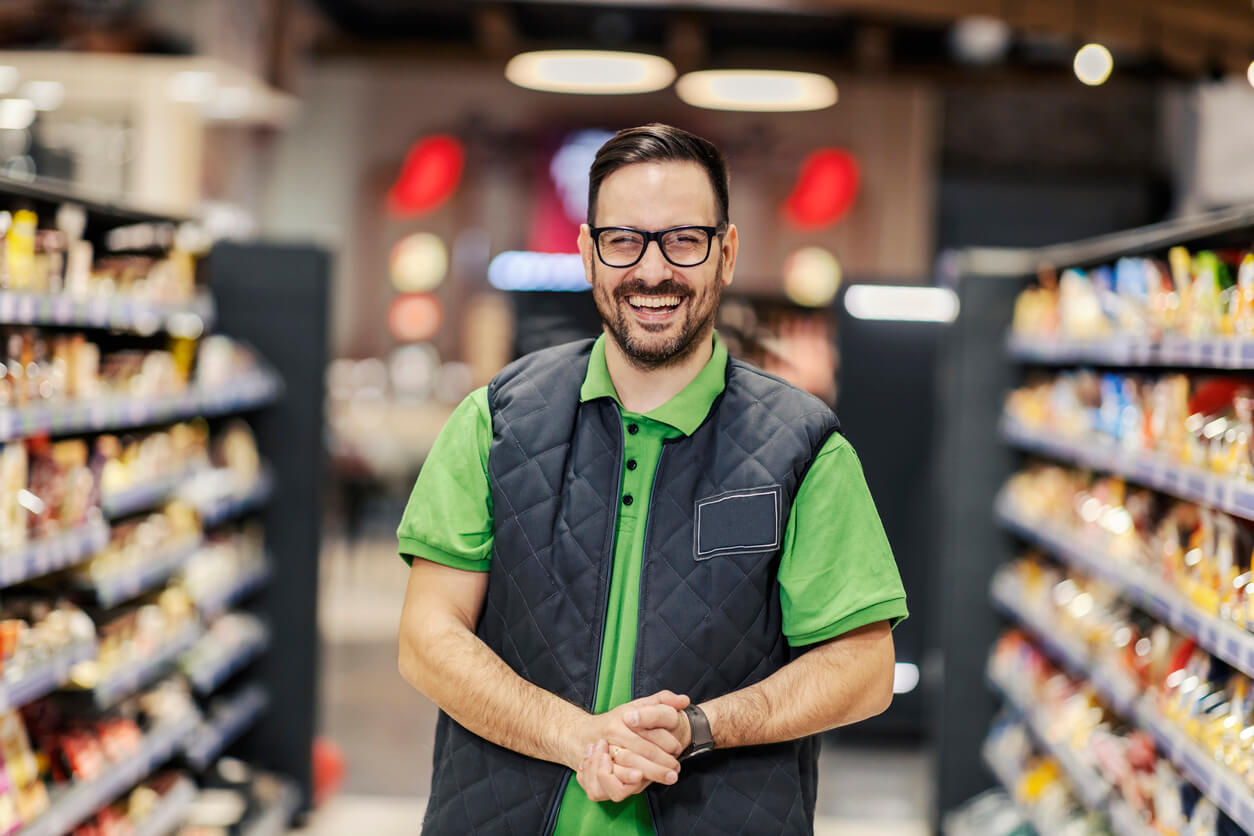
Stay informed
Sign up for our emails, and you’ll be the first to know whenever we discover new resources, develop new materials, and offer new training.